Чем сложнее, тем лучше
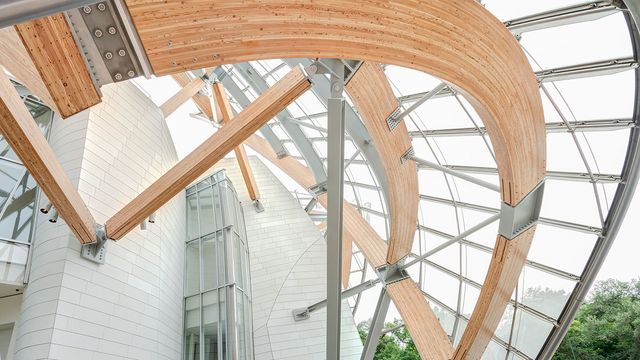
Музей Louis Vuitton в Париже — это буйство конструкций из стали, стекла и дерева. При проектировании и реализации необходимы были мужество и креативность — именно то, что может предложить Матиас Хофман и его компания Hess Timber.
Фирма Louis Vuitton известна во всем мире как производитель эксклюзивных чемоданов, дамских сумок и шампанского. Владелец марки — самый богатый француз Бернар Арно, поклонник искусства, который недавно решил построить на юге Парижа музей фонда Louis Vuitton. Проектированием занимался известный северо-американский архитектор Фрэнк Гери. Затраты на строительства были не так важны, а максимум внимания уделялся высшим требованиям к качеству и креативности по всем аспектам строительства.
Компания Hess Timber Матиаса Хофмана выиграла тендер на создание деревянных конструкций ломаной кровли сложной формы, состоящей из 12 «парусов». «Чем сложнее, тем лучше, я люблю такие проекты», — описывает свою философию этот профессионал из баварского Кляйнхойбаха. Благодаря своим необычным идеям и готовности к риску Матиас Хофман вошел в инженерную элиту в области деревянных сооружений. Ему немного жаль, что на задний план несколько ушел отличающийся большой конкуренцией обычный бизнес, — строительство несущих конструкций для стандартных залов. Крупные проекты требуют много усилий. «Каждый раз нужно практически новое оборудование» — говорит он, и это также относится к музею Louis Vuitton. Требуемые опоры коньков, часть из которых имеет двойной изгиб, изготовлены на самостоятельно разработанном прессе. Хофману удалось произвести впечатление на застройщиков в ходе размещения заказа благодаря необычному способу блочного склеивания на основе отдельных брусков. Изюминкой стали состоящие из брусков наружные ламели, которые обеспечивают одинаковый внешний вид сверху, снизу и с обеих боков.
А благодаря еще одной нестандартной идее Матиаса Хофмана — Hess Limitless — транспортировка клееного бруса длиной до 28 метров не привела к хаосу в Париже с его миллионами жителей. Этот метод основан на специальной геометрии склеивания. Он позволяет транспортировать несущие балки в виде коротких сегментов практически без ограничений по длине и потери несущей способности. Окончательная сборка производится непосредственно на стройплощадке. Используя оборудование WEINIG, Матиас Хофман может положиться на превосходного партнера. Для торцовки дефектов в компании Hess Timber используется станок SOLID CUT. Сращивание ламелей выполняют две линии SOLID JOINT PJ. В завершение на станке SOLID PROFILE P производится строгание для последующего склеивания. «Я никогда не сожалел о том, что выбрал оборудование WEINIG» — говорит Матиас Хофман.
Фотография: HESS-TIMBER / © Rensteph Thompson