Série SOLID PROFILE P de WEINIG : un éventail d'applications illimité pour une qualité parfaite
La moulurière est au cœur de la production. C'est ici que la valeur ajoutée est créée, lorsqu'un morceau de bois brut devient une baguette profilée. La série SOLID PROFILE P propose pour toutes les tailles d'entreprises - de l'artisan à la production en série industrielle - et pour toutes les applications, la machine optimale pour une production rentable. De la SOLID PROFILE P 700 à la SOLID PROFILE P 3000, les applications les plus diverses sont couvertes, qu'il s'agisse de fabrication de moulures ou de fenêtres, de rabotage de poutres, de fabrication de parquets ou de prérabotage. De par sa conception d'une grande modularité, la série SOLID PROFILE P s'adapte à toutes vos attentes en termes de qualité, de flexibilité et de performances et permet de concevoir des solutions personnalisées.
Avec l'aide de la commande intelligente de la machine, du positionnement automatique des arbres ou encore du système breveté PowerLock, jamais le pointage de la machine n'avait été aussi simple, aussi rapide et aussi sûr. De plus, une large gamme d'options vous permet de tirer le maximum de performances de votre moulurière. La SOLID PROFILE P est ainsi armée pour faire face à toutes les exigences, qu'il s'agisse d'usiner du bois massif, des matériaux dérivés du bois, des matières plastiques ou encore des matériaux composites.
La série SOLID PROFILE P est l'incarnation même de la qualité WEINIG, nourrie de plusieurs décennies d'expérience. Impossible de trouver meilleure assurance d'une production rentable à la hauteur des exigences actuelles du marché.
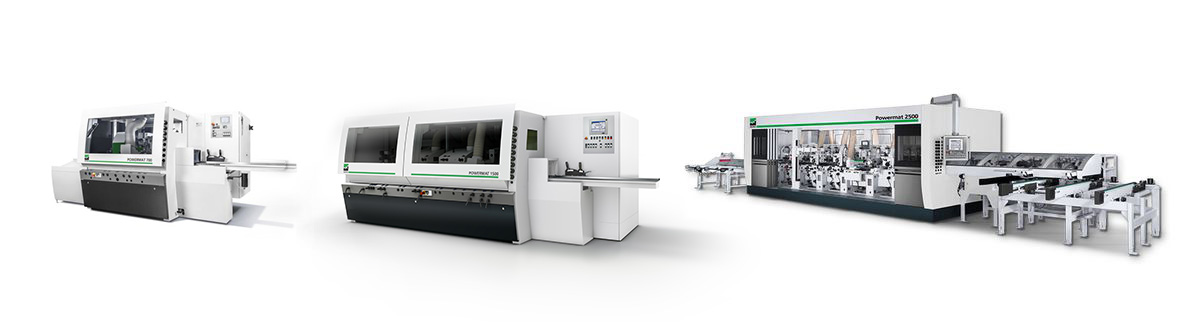
Toutes les machines
WEINIG SOLID PROFILE P 700
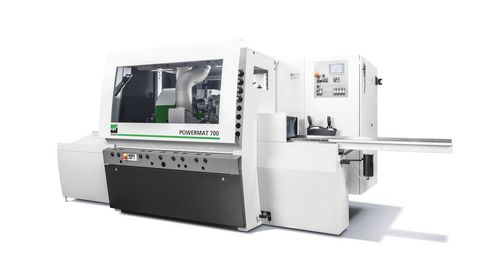
Rabotage et profilage de dernière génération
- Confort de conduite exceptionnel
- Gain énorme de temps sur le pointage
- Fidélité de répétition élevée
- Excellente qualité de surface
- Exploitation très efficace des ressources
WEINIG SOLID PROFILE P 1500
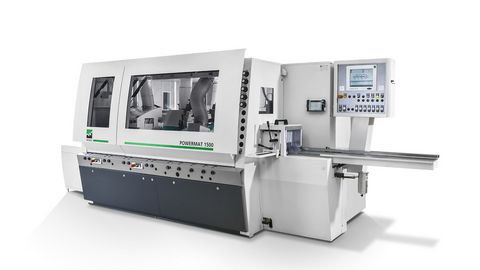
La moulurière polyvalente pour une rentabilité optimale
- Confort de commande inégalé
- Gain énorme de temps sur le pointage
- Fidélité de répétition élevée
- Excellente qualité de surface
- Exploitation très efficace des ressources
WEINIG SOLID PROFILE P 3000
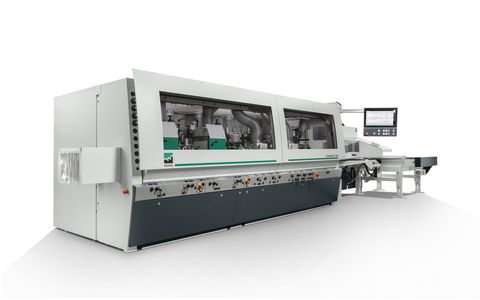
Fiable, performante, polyvalente
- Confort de commande inégalé
- Gain énorme de temps sur le pointage
- Changement rapide de dimensions et de profil
- Haute résistance à l‘usure
- Productivité accrue
Ce que vous offre la série WEINIG SOLID PROFILE P
- Technique de machine novatrice
- Grande précision de fabrication
- Haut niveau de sécurité du travail
- Construction modulaire
- Made in Germany
Références
Messages
Domaines d'utilisation
Moulures
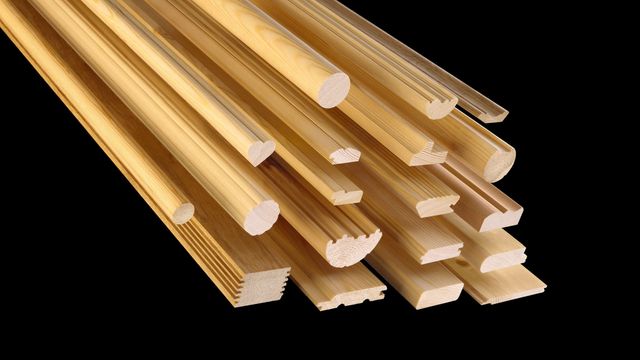
Notre cœur de métier
Le profilage de moulures de toutes sortes est depuis toujours le cœur de métier de WEINIG. Le profilage couvre un ensemble très large de produits finis qui posent tous les mêmes exigences en termes de technique de machine : une grande précision de profilage pour une qualité de surface irréprochable et un pas d'usinage régulier.
La technologie WEINIG définit sans cesse de nouveaux critères. Elle repose sur des bâtis de machines très robustes et des tables de machines très précises avec un guide parfaitement perpendiculaire. Les machines WEINIG révèlent toute leur supériorité dès lors que la dynamique entre en jeu : des arbres de grande précision circonférentielle, un système d'entraînement performant et des éléments presseurs parfaitement adaptés.
L'interaction parfaite entre ces composants garantit un transport de la pièce dans la machine à la fois régulier et très précis. Avec pour résultat la fameuse qualité WEINIG : une grande précision de profilage, une qualité de surface irréprochable et un pas d'usinage régulier.
Fabrication de fenêtres
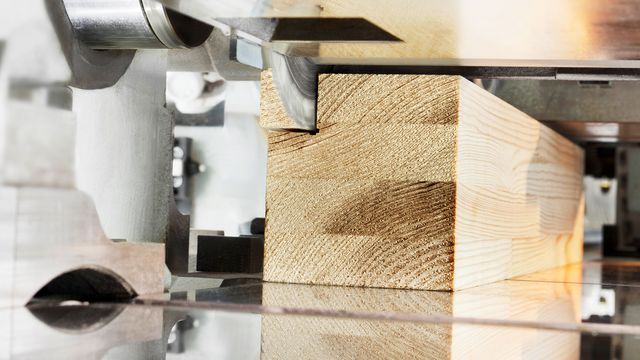
Trois étapes de processus sur une machine
Le profilage de carrelets de menuiserie en longueur et en bout ainsi que le fraisage et le perçage sont exécutés sur des centres d'usinage qui produisent les carrelets entièrement usinés. Mais la moulurière joue également un rôle important dans la fabrication de fenêtres, où elle est utilisée pour le corroyage des carrelets bruts, la séparation des parcloses brutes et le profilage des parcloses.
La WEINIG SOLID PROFILE P est équipée d'un pack de fabrication de fenêtres spécifiquement conçu pour réaliser ces étapes de travail. L'utilisateur peut ainsi choisir en appuyant simplement sur un bouton s'il veut uniquement raboter sur les quatre faces ou s'il veut aussi séparer la parclose brute. Des messages de confirmation de sécurité permettent de ne valider les réglages que lorsqu'aucune pièce ne se trouve dans la machine et d'éviter ainsi toute collision entre la lame de scie et les éléments presseurs. Avec le système PowerLock, le changement d'outils est réalisé en un temps record pour pouvoir profiler les parcloses.
Le système WEINIG permet en outre de mettre la moulurière en réseau avec la tronçonneuse et le centre d'usinage. WEINIG propose ainsi la solution idéale et la plus efficiente pour la fabrication de fenêtres.
Fabrication de palettes
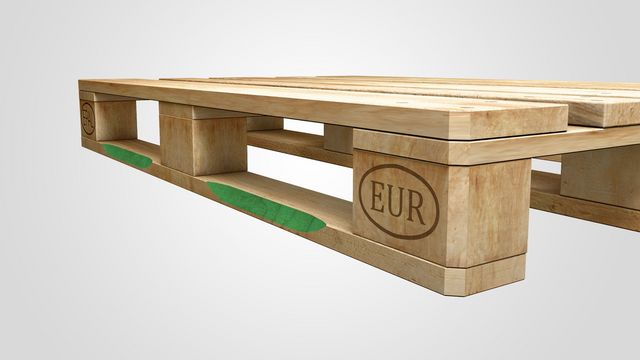
La palette Euro est devenue un outil incontournable pour le transport de biens et de marchandises. La fabrication de palettes est donc un segment de marché d'autant plus attractif. Les bois utilisés pour les palettes sont souvent non seulement rabotés sur les quatre faces, mais également chanfreinés pour faciliter leur prise par la fourche du chariot élévateur.
WEINIG propose une solution très efficace pour la fabrication de palettes : un arbre plongeant qui pénètre et ressort de la pièce. Un mesurage précis est donc nécessaire pour permettre à l'arbre plongeant de pénétrer et de ressortir au bon moment. Les paramètres de chanfrein, sa longueur et sa position sur la pièce, sont définis par l'opérateur.
Avec son mesurage précis et son arbre dynamique, cette solution WEINIG garantit que tous les chanfreins sont de longueur identique et à la même position sur la pièce. De plus, la longueur des parcours de plongée et de remontée est identique. WEINIG satisfait ainsi à toutes les exigences requises pour fabriquer des palettes de grande qualité de façon rentable.
Surfaces structurées
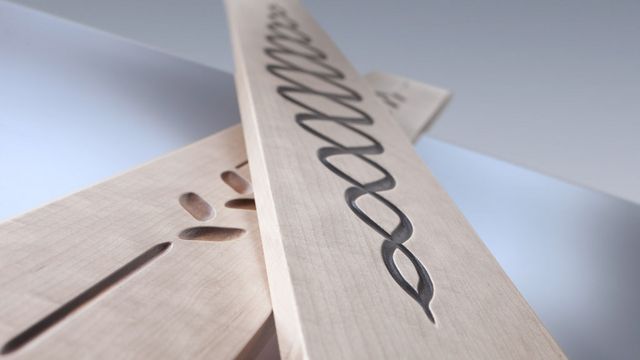
Fabriquer rentablement des produits novateurs
Les surfaces créatives ont le vent en poupe, que ce soit pour les devants de meubles, les parquets ou les façades. Ce qui nécessitait autrefois un travail fastidieux à la main ou un centre d'usinage peut être réalisé aujourd'hui au défilé sur une moulurière.
La technologie de rabotage structuré WEINIG permet aux arbres de se déplacer par rapport à la pièce en mouvement et d'obtenir ainsi une surface en trois dimensions. Il est possible au moyen d'un programme de CAO d'évaluer et de simuler préalablement la surface structurée avant de la produire sur la moulurière.
WEINIG se démarque ainsi une fois de plus et définit de nouveaux standards tout en vous donnant l'opportunité de conquérir de nouveaux marchés. Avec cette technologie, laissez libre cours à votre créativité pour concevoir de nouveaux produits en bénéficiant de temps de passe raccourcis, d'une grande productivité et de coûts à la pièce réduits.
Bois de construction massif
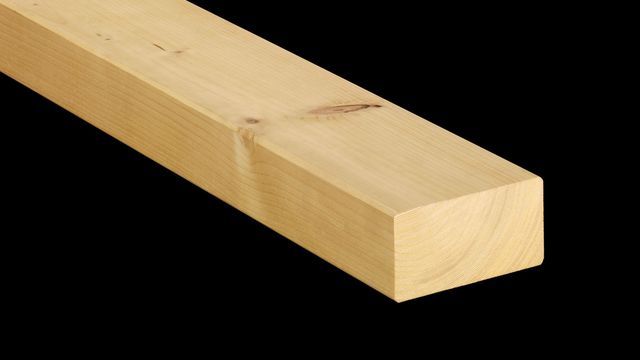
Ces dernières années, le bois massif utilisé comme matériau de construction est en pleine expansion. Il requiert une excellente qualité de surface, en particulier pour les éléments visibles. Le plus grand domaine d'application est celui des poutres, qui sont rabotées et chanfreinées sur les quatre faces.
WEINIG saura vous proposer la solution adaptée à vos exigences, de la petite machine à la grosse installation, avec toujours pour point commun la grande flexibilité garantie par l'unité de chanfreinage à 90°.
L'unité de chanfreinage sert à usiner le quatrième chanfrein de la poutre une fois que les autres chanfreins ont été créés avec les toupies verticales et l'arbre horizontal supérieur. La commande de l'unité de chanfreinage permet de changer rapidement de dimensions et de modifier l'épaisseur de chanfrein sans avoir à changer d'outil, uniquement par le positionnement des arbres.
Avec cette technologie, WEINIG permet aux petites exploitations d'être aussi rentables que les grandes entreprises.
Lamellé-collé
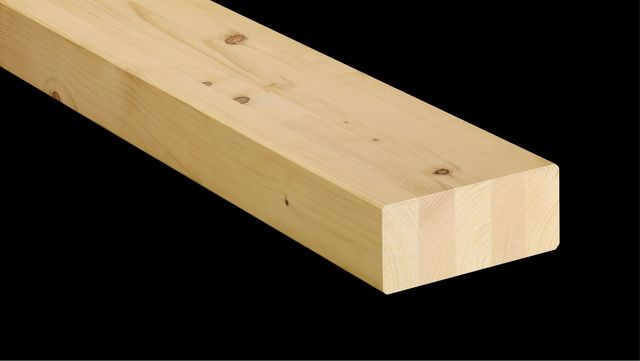
Rabotage de lamelles de lamellé-collé
Depuis quelques années, le lamellé-collé est de plus en plus utilisé dans la construction en bois, et le rabotage des lamelles qui le composent gagne donc en importance. L'objectif est d'obtenir des surfaces adéquates au collage à des vitesses d'avance élevées tout en enlevant aussi peu de matière que possible. Le gauchissement du bois ne joue aucun rôle ici puisque les lamelles seront ensuite collées avant d'être à nouveau rabotées pour la finition.
WEINIG propose une technologie de machine novatrice pour répondre à ce défi. La combinaison d'arbres horizontaux montés en biais et de toupies verticales flottantes permet de raboter les lamelles avec un enlèvement de matière minimal sur les quatre côtés tout en conservant le gauchissement du bois. Cette solution WEINIG augmente le rendement du bois et donc l'efficience des ressources.
Prérabotage
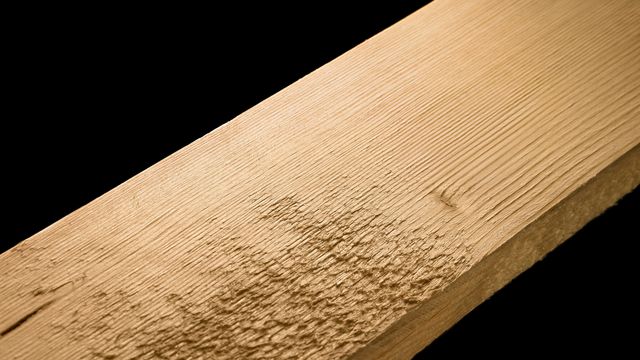
Le rendement du bois joue un rôle de plus en plus crucial dans l'usinage industriel. Des scanners sont donc utilisés afin d'identifier les éléments défectueux avant de les couper. Le prérabotage en début de chaîne est essentiel pour mettre à disposition du scanner une surface propre. L'enlèvement de matière doit donc être minimisé et, en règle générale, une vitesse d'avance élevée est exigée.
Dans ce segment, WEINIG propose aussi bien des solutions simples à un excellent rapport qualité/prix que des solutions novatrices aux technologies uniques : des outils à serrage hydraulique équipés de jointers aux arbres montés en biais et aux toupies flottantes, et ce, à des vitesses d'avance pouvant atteindre 300 m/min. Bien sûr, WEINIG dispose également des mécanisations adaptées à chaque technologie de machine. Vous voici parfaitement équipés pour le prérabotage !
.