Edgebander ACCURA 1556: The new top class with superior performance
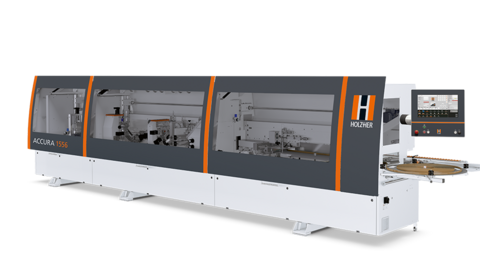
The ACCURA 1556 premium model with two cutter units allows processing of solid wood edging with thickness up to 15 mm (optional 20 mm). The ACCURA 1556 grooving serves for fully automatic grooving in the vertical and horizontal direction. With this machine, the groove position and groove depth can be set fully automatically on two NC servo-axes. The standard equipment on the ACCURA 1556 flex includes a corner buffing unit for perfect edge finishing without any subsequent work.
Different requirements - different prices
The price of a HOLZHER machine is just as individual as your requirements are. Therefore, let us discuss briefly what is most important to you – you will then receive our preliminary, non-binding quote.
Unterschiedliche Anforderungen – unterschiedliche Preise
Der Preis für eine HOLZ-HER Maschine ist so individuell wie Ihre Anforderungen. Deshalb besprechen wir am besten kurz, was Ihnen wichtig ist – und schon bekommen Sie ein erstes, unverbindliches Angebot von uns.
* Erforderliche Felder
Personal advice – for higher productivity and greater efficiency
Together with your HOLZHER expert you will find the ideal machine for your requirements. Simply submit the completed form, and your local HOLZHER expert will be happy to discuss all further details with you.
Here is what the HOLZ-HER ACCURA offers
- Invisible Joints with Glu Jet Thin Film Technology
- Integrated Multifunction Cutting Technology
- iTronic for intelligent automation
- Workpiece Thickness up to 60 mm
- Edge Thickness up to 20 mm
- Units for 100% Repetition Accuracy
Here is what the HOLZ-HER ACCURA 1556 offers
Technical Details
iTronic for intelligent automation
iTronic operating components
1. Adaptive trimming blade
Full adaptive trimming blades with automatic pressure adaptation to match edge thickness and height. Your advantages:
- Always the right pressure for different types of edging
- Prevents unnecessary vibration
- Reduces wear
2. Automatic pressure unit
The contact pressure of the individual pressure rollers is adapted perfectly to the application by an intelligent pneumatic system. Your advantages:
- Reduces reject quotas to a minimum
- Eliminate sample workpieces
- Optimum machining results even for continuously changing applications
3. Automatic glue quantity control
Automatic, requirement-adapted control of glue quantity with program selection: Always optimum glue application for:
- Various types of panels, e.g. chipboard or MDF
- Various panel thicknesses
- Various feed rates
- EVA or PUR glue
- Adaptation to processing parameters for glue from different manufacturers
4. Automatic cleaning routine
Integrated, fully-automatic purging routine for PUR glue at the touch of a button on the control. This process completely purges the machine, full automatically, with the correct quantity of cleaner, at the right temperature and contact pressure. (Cleaning is required after 48 h = PUR reaction time). Your advantages:
- Best system on the market
- PUR glue always under control
- Avoids errors during cleaning operation
5. Remaining glue quantity indicator
The remaining quantity of glue as well as the running meters that can still be processed are automatically monitored by a special sensor in the system and displayed to the operator on the control. Your advantages:
- Operator knows how many running meters can still be produced at all times
- Professional supervision of the cleaning process
- Optimization of remaining quantity of glue in system at time of cleaning process.
fa.s.t. setting technology
fa.s.t. or "setup in the gap" is one of the major themes for efficient edging operations. fa.s.t. enables you to run different machining processes at the same time on the edgebander. For example, it is possible for the operator to switch on the corner rounding unit intelligently, without having to empty the machine for the set-up procedure.
Edge Control
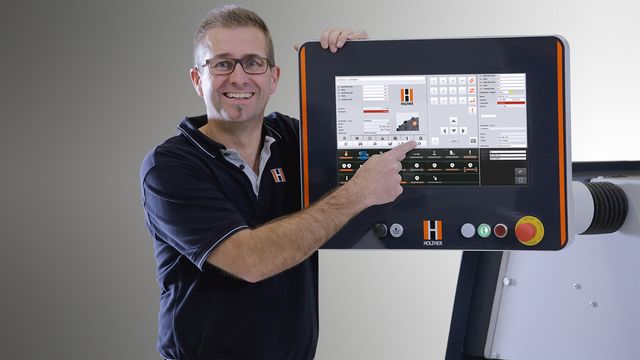
Edge Control
21.5" Touch screen color monitor with 16:9 format. High performance control with simply operation for rational machine set-up and change-over.
- 21.5" touch screen color monitor - standard feature.
- Graphic user interface, all information displayed in plain text and/or graphic form.
- Simple operation – rotating and swiveling control panel at eye height.
- Programs are simple to call with program names and numbers.
- Large program memory for all desired applications.
- Individual selection of units with the functions as basic setting possibilities for nominal values, path points and tool corrections.
- Service reports in clear text.
- Individual management for up to ten users with password protection and individual authorization.
- Network connectivity.
- Online maintenance, rapid exchange of data with HOLZ-HER service department.
- Barcode interface.
SYNCHRO edging feed
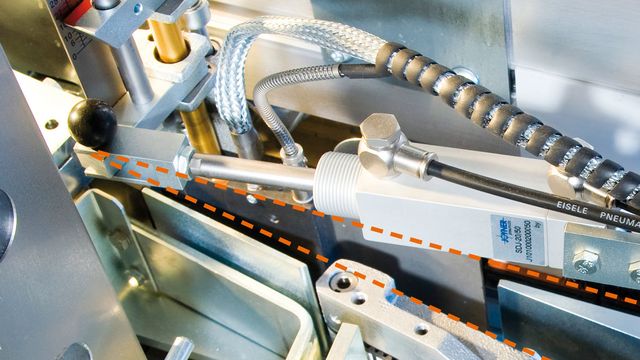
Edging magazine SYNCHRO drive.
With its synchronous adaptation to the feed rate, this edging magazine guarantees short intervals between workpieces and simultaneously optimizes edging protrusions.
Small feed angle thanks to nozzle design - easy feeding of solid wood edging up to 20 mm.
Jointing cutter
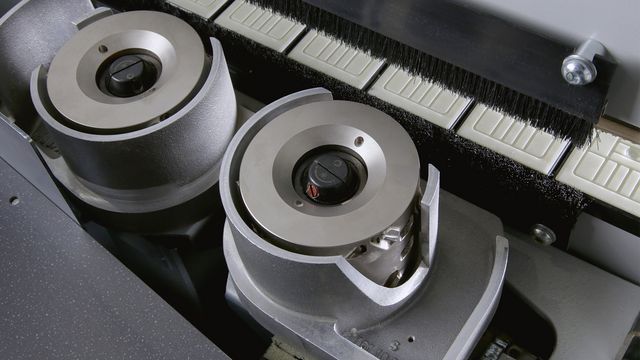
Cut edgings often have small tears in the top layer. The jointing cutter unit ensures perfect glued surfaces and prepares the panels for the gluing process. Equipped with two 70 mm dia. diamond tipped cutters with AirStream technology (HOLZ-HER / LEUCO Patent). Including HSK32R chuck. For greater rotary precision, to provide smoother running, longer service life and preserve tools and motor.
With symmetrical diamond tipped cutters (dia. 100 mm) for maximum joint quality and long service life. Automatic height adjustment with two NC servo-axes.
Glu Jet automatic - glue application system
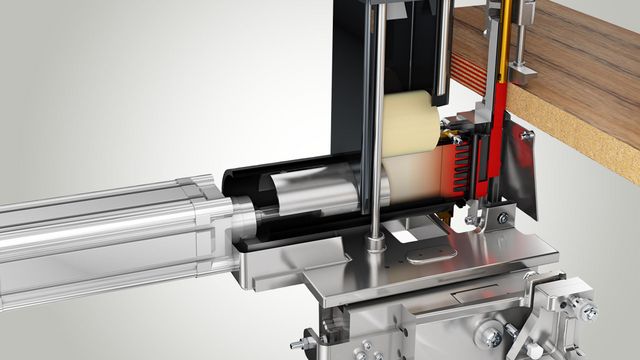
Automatic replenishment
- The pressure cylinder presses the cartridge or granules against the heater elements. After reaching a certain position, the sensor sends a replenishment signal to the control. As long as glue is being applied to a workpiece, charging is delayed until the work is finished. The pressure cylinder retracts automatically, a new cartridge or fresh granulated material is gravity fed from the cartridge supply shaft into the heating chamber where it is again pressed against the heating elements.
- Purging hole for automatic cleaning system – e.g. cleaning out PUR glue.
The Glu Jet automatic is attached to a set-up carriage alternating with the LTronic unit as a glue application system with automatic change-over. Change-over is accomplished within a maximum of two minutes by a high precision interface with HSK chuck and CNC technology.
Motor-driven pressure unit
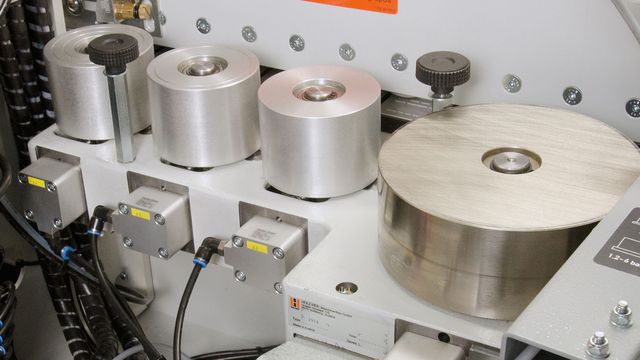
Synchronously driven pressure unit with automatic adaptation to feed rate and NC servo-axes for motor-driven adjustment to correct edge thickness. Straight and tapered pressure rollers for perfectly glued joints.
Trimming unit
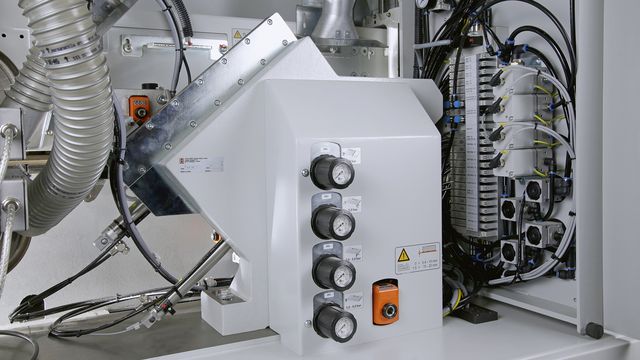
Most powerful trimming unit in its class – edge cross-section 20 x 65 mm. With hardened linear guides for high precision trimming results up to edge thickness of 20 mm.
Flush cutting unit
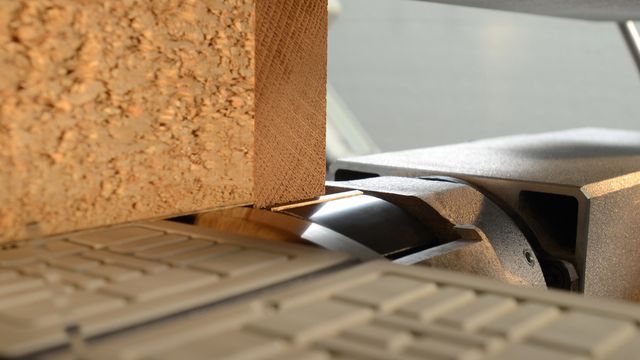
High performance cutter unit for edge thickness up to 15 mm. Two NC servo-axes for cutting with and without edge protrusion. Standard on ACCURA 1556 premium and 1558 performance.
- Edge thicknesses up to 20 mm (optional).
Cutter unit
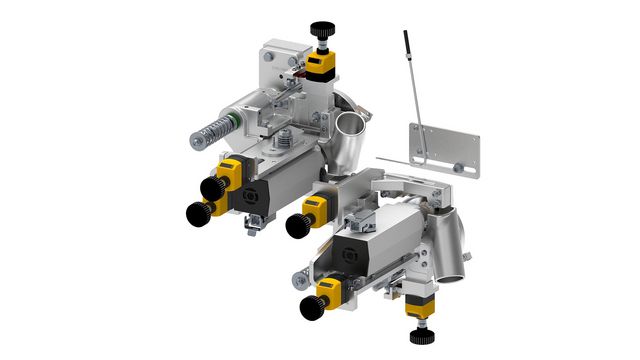
Heavy duty floor-mounted machine with shock-absorbing mounts and large sensing rollers for perfect results even at high feed rates.
100% repetition accuracy at the touch of a button based on zero-clearance mechanisms and six high precision NC servo-axes. Horizontal sensing with angular sensing rollers with chemically applied nickel plating developed especially for processing modern, high gloss edging.
- In multifunction package with multistage tool.
Shaping cutter unit
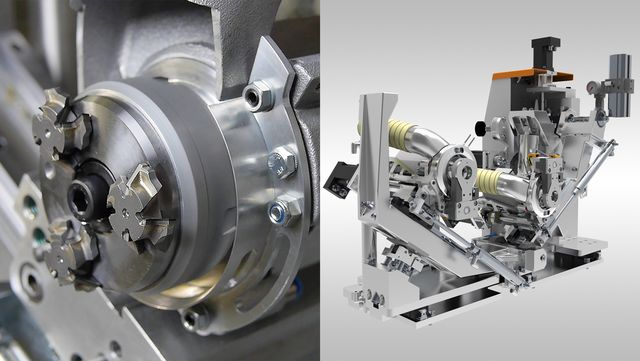
Shaping cutter unit with four NC servo-axes as standard feature
Uncompromising shaping cutter unit for workpieces with thicknesses up to 60 mm.
Unit adjustment on linear guides. With standard blast nozzles in front of sensing rollers to blow away chips in front of sensing areas. Including shelf program for optimum processing of shelves with rounded edges.
Automatic pendulum sensor copies ends without material protrusion and leaves the optimum longitudinal edge protrusion for subsequent machining with the radius scraper.
- In multifunction package with revolving tools.
Scraper unit
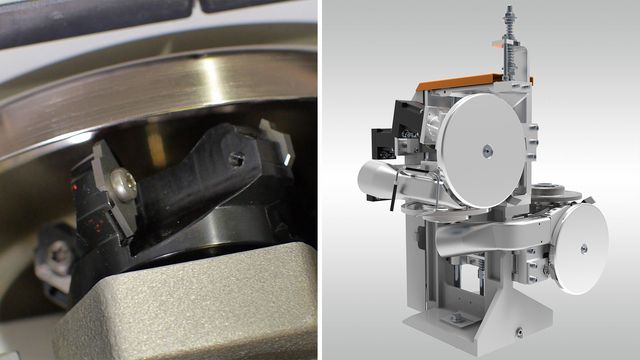
100% repetition accuracy at the touch of a button based on zero-clearance mechanisms and six high precision, fully digital NC servo-axes.
Including high gloss package for exact adjustment of tool depth when using high gloss panels with protective foil as well as sensing rollers with chemical nickel plating.
- In multifunction package with revolving tool magazine for 5 tools.
Flat scrapers with pre and post-sensing
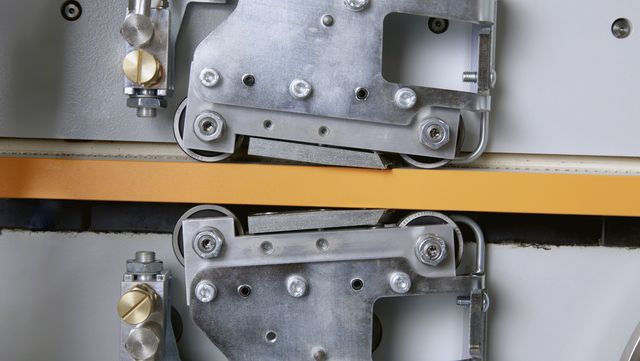
Clean surface finishing with pre- and post-sensing for high feed rates. 2 HW cutting edges, for use on 4 sides. Completely eliminates all manual finishing. Both units can be lifted automatically for special applications.
Buffing unit
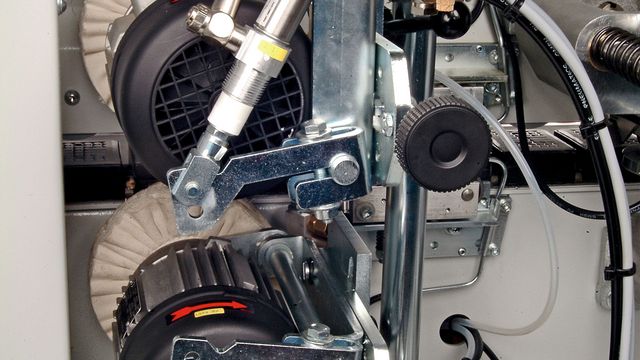
Polishing for maximum gloss; for complete finishing. Standard setup.
- Also available as oscillating version
Corner buffing unit
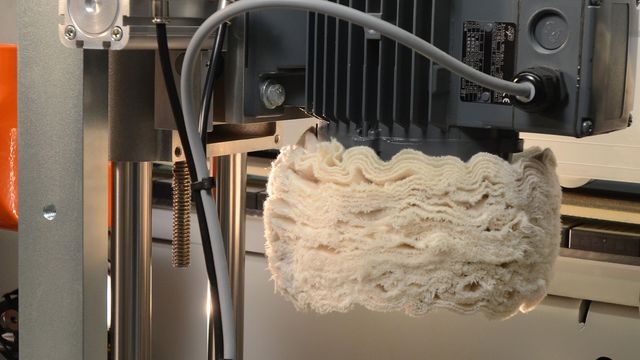
For a perfect finishing on edging ends. Completely eliminates all manual finishing. Including plunge control and motor-driven horizontal adjustment via NC servo-axes.
Grooving unit
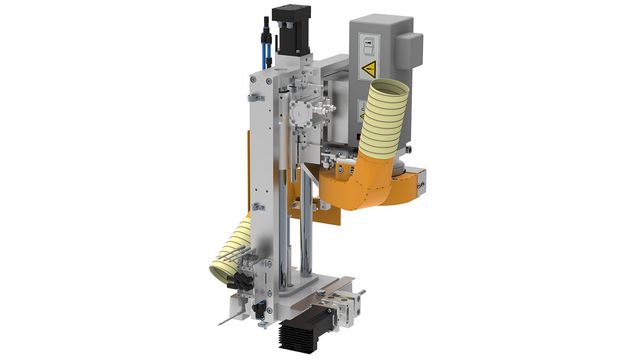
Forward-direction grooving, with two NC servo-axes for groove depth adjustment as well as groove position above control panel as a standard features. Swivels 0 to 90 degrees Including plunge control.
Technical Details
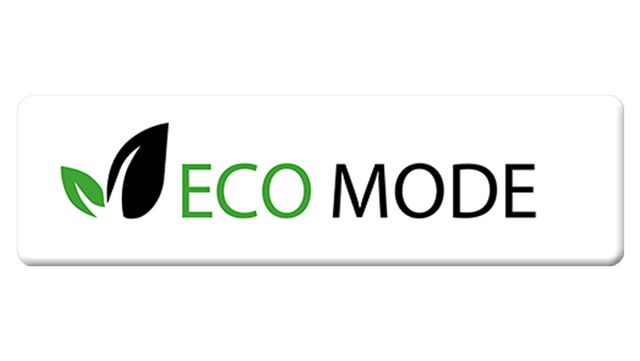
Energy savings made easy
The intelligent ECO Mode energy management for HOLZ-HER edgebanders not only helps preserve our environment - it also saves you money.
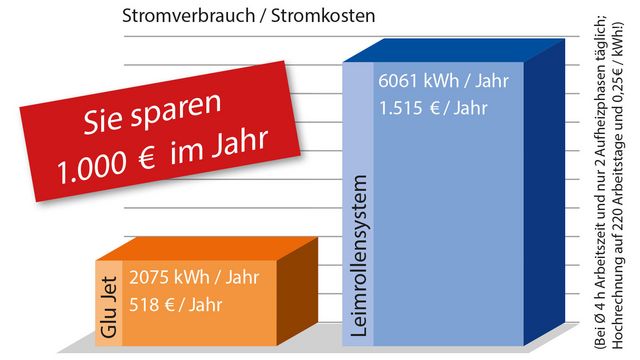
Are You Already Saving?
Are you still "rolling" glue or are you already saving? Savings of up to € 1,000 / year with our patented Glu Jet nozzle system.
References
Further information
Brochures
Simple, fast and sustainable: more details in a downloadable PDF document.
Brochure Edgebander ACCURA | LUMINA (PDF, 6 MB)