HOLZ-HER DYNESTIC Series: Time savings in production with HOLZ-HER nesting technology
HOLZ-HER has its brand new nesting technology on the market. Get all information about the innovative nesting CNC machining centers DYNESTIC 7532, DYNESTIC 7507 and DYNESTIC 7505. All three machining centers have a high automation capability and are available in different equipment variants.
HOLZ-HER's nesting technology ensures efficient formatting and drilling on one machine. Here the panel is held by large-surface vacuum on a wear plate. The great advantage of this production method is production of exactly formatted workpieces, already provided with groove or rebate in the rear wall and all required vertical holes for shelves, connectors, etc. Above all the entire process is accomplished without additional handling work and is therefore extremely efficient in terms of time and resources.
The essential prerequisite for nesting is, however, that the proper software be fully integrated into the machining process. Here HOLZ-HER offers a free-form solution for stairs and frame constructions as well as a purely rectangular nesting feature. With its versatile import possibilities for highly differing nesting modules as well as complete graphic control surface and barcode interface, the machine is optimized for comprehensive applications.
HOLZ-HER's nesting CNC machining centers allow cut-optimized machining and cutting on panel materials. The automation components for material handling makes the DYNESTIC series even more efficient.
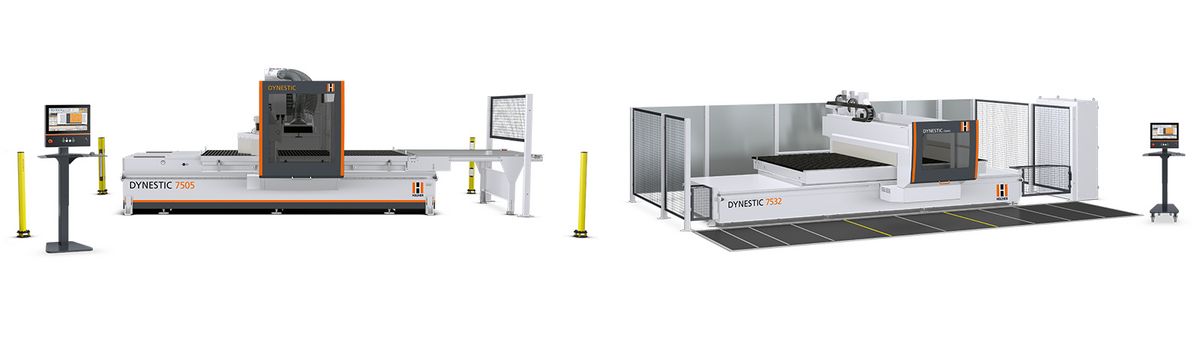
All machines
HOLZ-HER DYNESTIC 7535
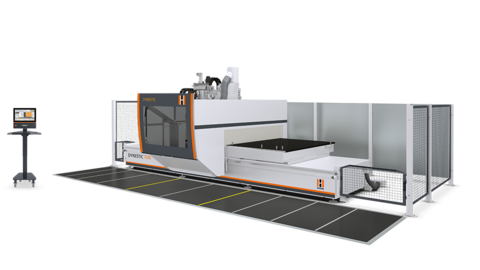
Dynamic 5-axis machining in XXL format
- Automation components
- Solid gantry design
- Machining in Y direction: up to 2,200 mm
- Machining in X Direction: Up to 3,700/4,600/6,250 mm
HOLZ-HER DYNESTIC 7532
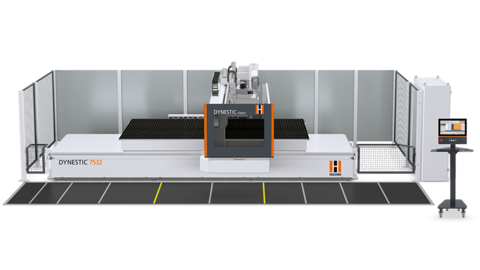
High-end gantry CNC machining for nesting and much more
- Automation components
- Solid gantry design
- Machining in Y Direction: Up to 2200 mm
- Machining in X Direction: Up to 3700 / 4600 mm
HOLZ-HER DYNESTIC 7507
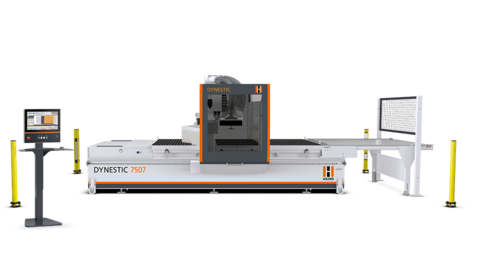
Intelligent and future-oriented nesting processing
- Solid gantry design
- Machining in Y Direction: Up to 2200 mm
- Machining in X Direction: up to 3100 / 4600 mm
HOLZ-HER DYNESTIC 7505
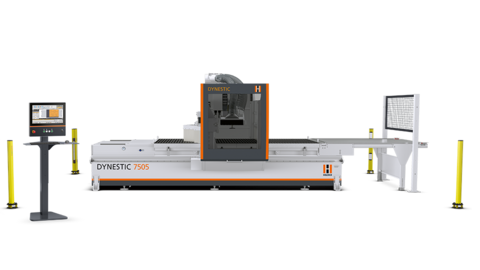
High-efficient panel processing with the latest nesting technology
- Solid gantry design
- Machining in Y Direction: Up to 1580 mm
- Machining in X Direction: up to 3100 / 3700 mm