WEINIG Gluing presses: The production process of the future
Glue solid wood and increase your added value! By increasing the depth of production but also by possible processing scrap wood.
We are continuously developing and improving our systems and machines to meet your needs of your production process. For an optimum added value, panels are produced perfectly aligned as a result of an intelligent pressing process. This helps save material, minimizes post-processing and saves you money. In addition, the glue is applied in a very precise way, which helps to save glue and to reduce cleaning. This guarantees a smooth and secure production process. Automatic feeding systems and high frequency technology that reduce curing times, e.g. for PVAc, to a minimum, are provided as standard.
A variety of applications – from floorings to traditional furniture and DIY panels to mini beams - WEINIG offers you the perfect technical solution out of its portfolio of gluing presses.
All machines can be optimally equipped for each individual application. This includes, for example, various gluing systems, pre-cutting solutions, mechanizations and equipment for modern glue systems.
WEINIG SOLID PRESS L
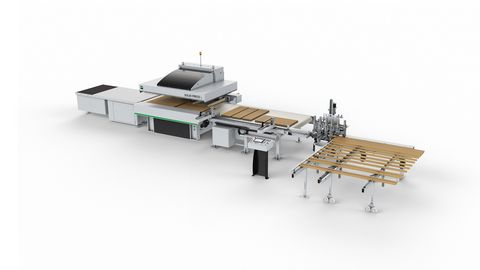
The compact high-frequency gluing press for industry and trade.
- Multiplication of the daily capacity compared to manual gluing
- Extremely efficient input of high-frequency energy in the glue joint.
- Extremely user-friendly and maximum flexibility
- Mechanization and automation solutions are available as options.
- The best gluing and panel quality
WEINIG SOLID PRESS T
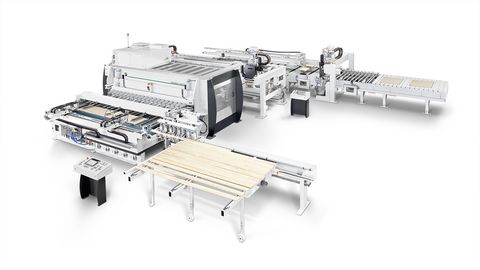
Perfectly adjusted, the upper mid-range
- Efficient even with small batch sizes
- Unlimited panel width possible
- Optimum machine utilization at all times as a result of a system that is not dependent on width
- Low post-processing as a result of minimum additional sanding
- Modular combinations possible - even after purchase!
WEINIG SOLID PRESS C
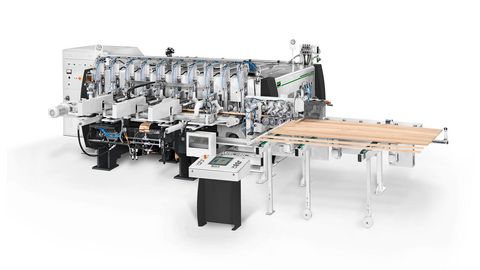
The very best. Non-stop high-performance
- Very high performance potential
- Perfect surface quality
- Maximum precision of machine and end product
- Convenient and user-friendly
- Best integration into existing, productivity-enhancing WEINIG system solutions
WEINIG SOLID PRESS B
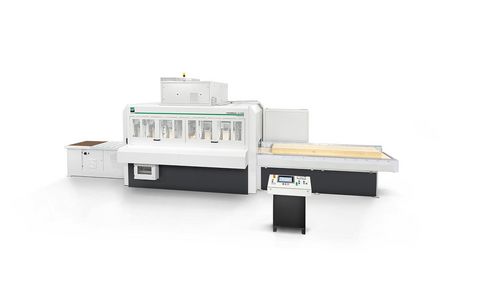
High-frequency gluing press for window scantlings, beams and panels
- High performance thanks to short cycle times
- Intelligent high-frequency heating technology for a perfect gluing and product quality
- Comfortable and safe handling
- High-frequency shielding with lowest radiation values to guarantee high working safety
- Modular system - upgrades possible
WEINIG SOLID PRESS X
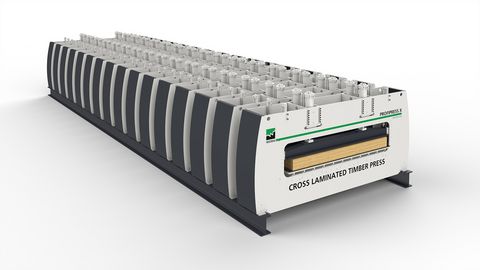