WEINIG rip saws: Strong solutions to make your cutting even more profitable
Width cutting, generally referred to as ripping, combined with longitudinal cutting, represents the first processing stage in all solid wood processing. Thus, it constitutes the foundations of efficient and modern production. Errors in (width) cutting, such as wood losses, missing quantities or excessive stock levels permeate the entire subsequent production process and have a lasting, negative effect on operating results.
Modern and efficient cutting is, therefore, indispensable. WEINIG provides optimal machine concepts to fulfill this requirement. From the small workshop to the fully-automated production line.
WEINIG SOLID RIP U
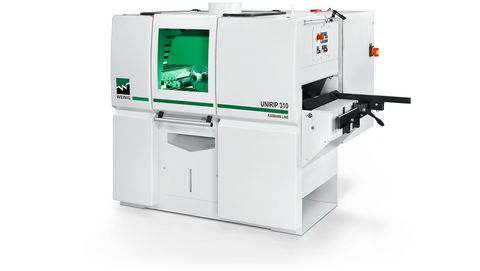
Multi-blade rip saw with Quickfix.
- Perfect cut quality
- Short setup times
- Quickfix
- Easy to operate
- Low space requirements, compact design
WEINIG SOLID RIP V
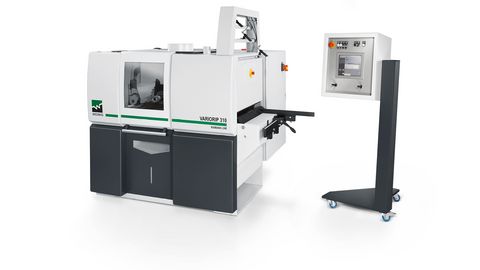
Multi-blade rip saw with up to 2 adjustable saw blades
- Perfect cut quality
- Up to 2 automatically adjustable saw blades
- Quickfix
- Short setup times
- Easy to operate
WEINIG SOLID RIP P series

High-performance multi-blade rip saw for all requirements.
- High performance potential
- Maximum stability and productivity — even with extreme loads
- Glueable cut
- Outstanding user-friendliness
- SafetyPlus anti kick-back device
WEINIG SOLID RIP FX 210
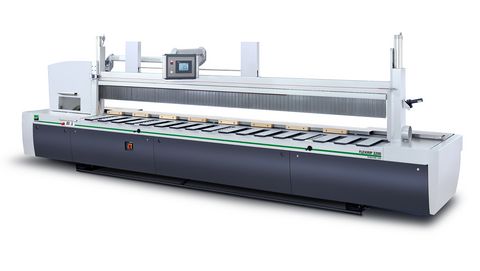
The longitudinal circular saw for flexible cutting in operations from the small workshop to industrial series production.
- Efficient and powerful ripping
- Optimum material yield
- Comprehensive safety concept
- Can be integrated in pre-cutting systems
- Innovative mechanical engineering