Optimizing cross-cut saw SOLID CUT TF 2600: Efficient performance through intelligent solutions
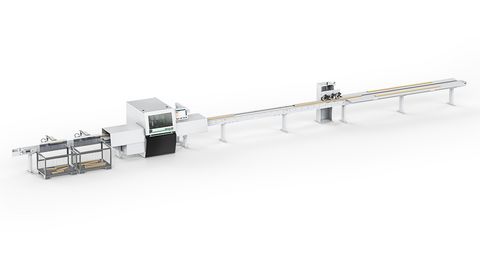
High performance without compromising on standards is the advantage that the SOLID CUT TF 2600 offers you. Independently-driven measuring wheels only measure when the wood is in motion. Uncontrollable slippage or belt elongation in the infeed system do not distort the cutting results as the machine cuts at precisely the intended point. This avoids errors with good quality wood and guarantees precise fixed lengths regardless of the wood quality. Standard conveyor belts reduce the operating costs of the machines, which are profitable all-round.
Different requirements - different prices
The price of a WEINIG machine is just as individual as your requirements are. Therefore, let us discuss briefly what is most important to you – you will then receive our preliminary, non-binding quote.
Personal advice – for higher productivity and greater efficiency
Together with your WEINIG expert you will find the ideal machine for your requirements. Simply submit the completed form, and your local WEINIG expert will be happy to discuss all further details with you.
The WEINIG SOLID CUT TF 2600 provides
- VarioSpeed infeed belt as standard
- 5 driven feed rollers from below, pressure rollers from above
- Pneumatic saw stroke
- Cutting of cross-sections up to 260 x 12 mm or 160 x 80 mm is possible
- Saw blade diameter 500 mm
- Integrated waste gate as an option
- Measuring wheel in front of saw blade
- Min. fixed length behind saw blade: 140 mm
- Cutting tolerance ± 0.8 mm to 1000 mm length
Technical Details
Increased profitability
Our optimizing cross-cut saws offer high performance potential in every respect. To maximize this potential, the intelligently controlled VarioSpeed, among other things, reduces the spacing between consecutive workpieces as much as possible. The SOLID CUT thus provides a continuous supply or workpieces, so that the idle time of the machine is minimized. This increases the efficiency and productivity of the optimizing cross-cut saw.
Highest value
Cross-cutting is one of the most important procedures in solid wood processing, because it is at the cutting stage that the quantity of wood available for further processes in production and the quality of the final product are determined. Even in its standard version, the SOLID CUT TF 2600 offers full optimization of the incoming material, i.e. the measurement of the entire workpiece is carried out independently of the drive and slippage before the first saw cut. The operator only marks the defects and/or different qualities, and the optimizing cross-cut saw does the rest, always focusing on a maximum yield and/or the highest material value. Finger-jointing lengths are fully integrated into the optimization and up to 8 different wood qualities can be classified.
Dynamic feed
The wide feed rollers hold the wood securely. The rollers are deeply embedded in the table, preventing tipping of short lengths and maintaining straight, precise cutting. Individually cycled pressure rollers from above create the required counter-pressure for rapid and precise positioning without correction runs the impact performance. The pressure rollers only lower after the start of the board, meaning vibration-free and low-wear operation. The strong drive unit guarantees high long-term performance.
Future-oriented and flexible
Adjust the SOLID CUT to your individual needs, for different wood qualities have different requirements. That is why WEINIG offers the right equipment package for every application including suitable pressure and feed rollers with different surface coatings, which can be changed in a short time if necessary.
Secure workpiece guidance
From the marker table to sorting, the SOLID CUT guarantees continuous and secure workpiece guidance. For example, inside the cross-cut saw, a continuous fence ensures a clean and exact alignment and a right-angled cut of the workpieces.
Options for extension
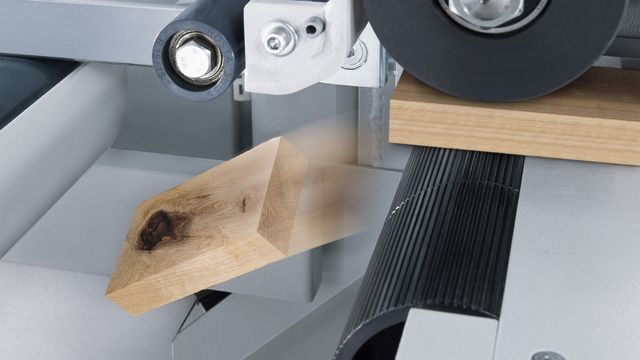
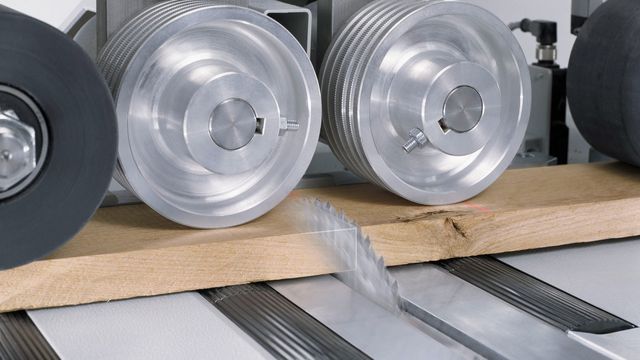
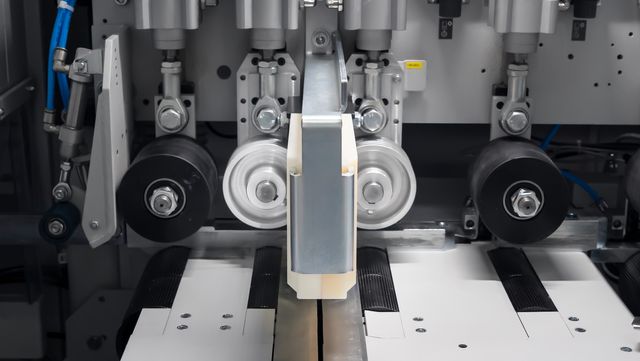
Equipment package for increased accuracy
Increase in length accuracy for fixed lengths up to 1000 mm
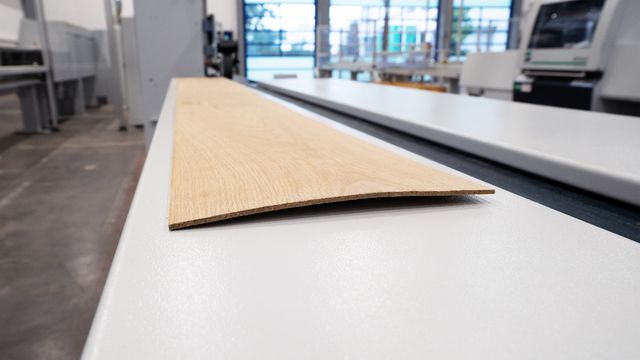
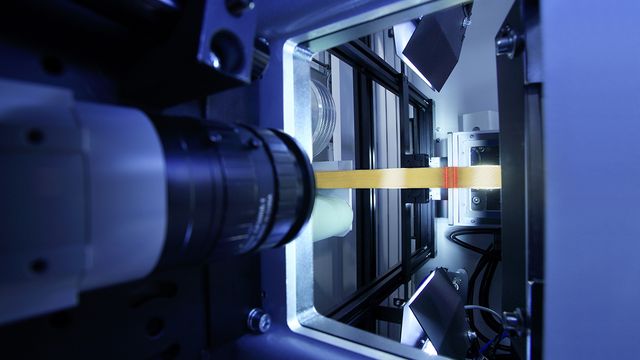
WEINIG scanner systems
Workpiece properties can be detected fully automatically and during production. Cutting is then performed automatically based on the data obtained.
Further information
Brochures
Simple, fast and sustainable: more details in a downloadable PDF document.
Download brochure