WEINIG SOLID PROFILE H series: Stability and flexibility in outstanding combination guarantee perfect surface quality with high productivity
WEINIG high-speed planing machines offer uncompromising performance. In no time at all, you can convert a stack of timber into high-quality workpieces. The Highspeed series is the top performance league in terms of design and processing. This means planing and profiling at feed speeds of up to 300 m/min with excellent surface quality.
WEINIG high-speed planing also means efficient production in batches large and small. In addition, you will benefit from safety based on strict quality standards, high ease of use and naturally, top service from the world market leader.
What are your requirements? It’s all within your grasp. Make your choice from our application-oriented range. From the SOLID PROFILE H 3000 entry model to the SOLID PROFILE H 4300 powerhouse. And we can help to configure the machine to suit your individual production requirements with automation systems, tools, measuring systems, adjustment aids and grinding machines. Everything from a single source.
All machines
WEINIG SOLID PROFILE H 3000
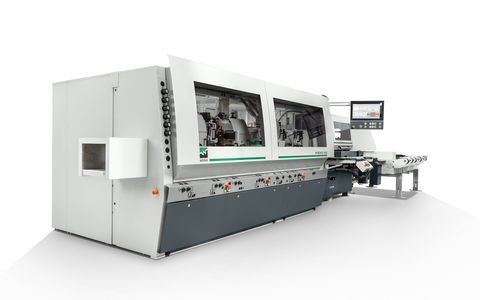
The robust moulder for entry into the SOLID PROFILE H series
- High wear resistance
- Rapid dimension and profile changes
- High level of repetition precision
- Outstanding surface quality even at high feed speeds.
- Highly user-friendly
WEINIG SOLID PROFILE H 4000
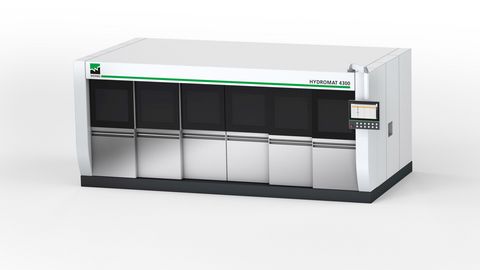
The powerful machine for high-speed applications
- Tremendously high productivity
- Outstanding surface quality even at high feed speeds.
- High wear resistance
- Innovative machine control
- Sustainable machine concept
The WEINIG SOLID PROFILE H series provides
- Solid and robust construction
- Integratable in system solutions
- Very high performance potential
- Modular design
- High level of work safety
Areas of application
4 sides planed
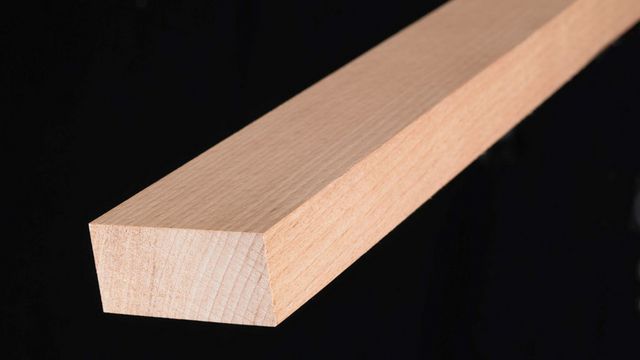
Perfectly right-angled work pieces
Wood is a natural material and that influences the requirements that are involved for processing it. Wood can contain defects, it can be bent or warped. For many applications, therefore, e.g. for furniture, it is essential that the work pieces are planed on all four sides. The key thing here is that the work pieces are accurately straightened and that they have perfect angles after being processed.
This may sound easy, but in many cases it is not, because the production precision of the machine has a significant influence on the quality of the end product. You can always rely on the famous WEINIG quality. WEINIG offers many different solutions, from manual to fully automatic operation and from machines for occasional use to machines in continuous shift operation.
Construction timber
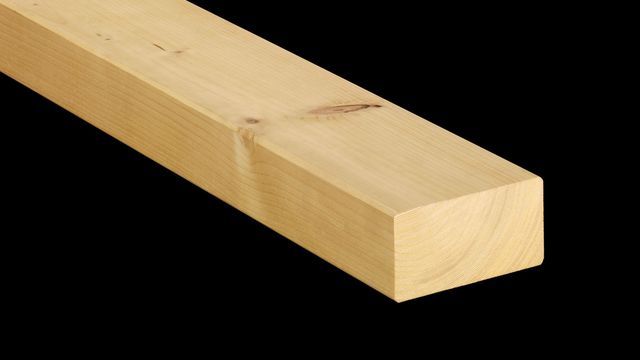
The importance of solid wood as a construction material has grown constantly over the last few years. This means that there are high demands on the surface quality, particularly for the visible areas. The largest area of application are beams, which are planed on 4 sides and chamfered.
Depending on your requirements, WEINIG offers the right solution, from a small machine to a large line; but they have one thing in common: a high level of flexibility because of the 90° chamfering unit.
The chamfering unit is used to produce the fourth chamfer on the beam after the other chamfers have been produced by the vertical spindles and the horizontal top spindle. The chamfering unit control means that dimensions can be changed quickly and a change in the strength of the chamfer can be made without changing the tool and simply by positioning the spindles.
With this technology WEINIG enables small companies to work with the same economy as a large organization.
Glulam
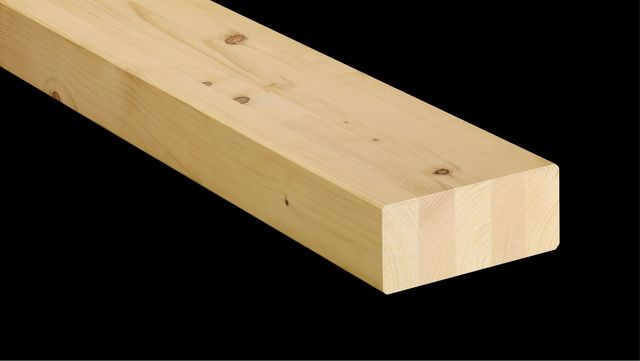
Planing glulam lamellae
Glulam is increasingly being used in recent years and therefore more and more importance is being given to planing glued laminated timber lamellae. This depends on achieving a glueable surface at high speed with the lowest level of chip removal. Even the curve of the timber does not make a difference, and can be kept, because the lamellae are glued afterwards and then finally planed again.
WEINIG meets this challenge with innovative machine technology. The combination of slanted horizontal spindles and floating vertical spindles allows the lamellae to be planed with a minimum of chip removal on all four sides while maintaining the curvature of the wood. These WEINIG solutions increase material yield and thus also resource efficiency.
Pre-planing
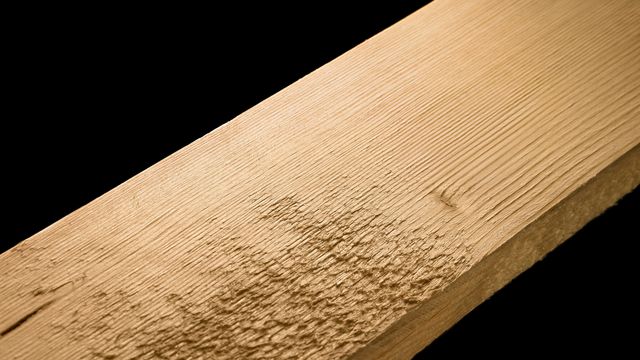
In industrial wood processing, material yield plays an ever greater role. Scanners are used in this context to identify places with defects and to cut them out. Pre-planing is necessary at the start of the entire chain in order to provide the scanner with a clean surface. Accordingly, chip removal should be minimal and a high feed speed is usually required.
In this segment, WEINIG offers both simple solutions with excellent value for money, as well as innovative solutions with unique technology: from hydro-tools to jointers, slanted spindles and floating spindles up to a feed speed of 300 m/min. As well as the necessary machine technology, WEINIG, of course, also offers suitable mechanization. We can meet your pre-planing needs perfectly!