WEINIG SOLID PROFILE P 700: The new generation of moulding and planing
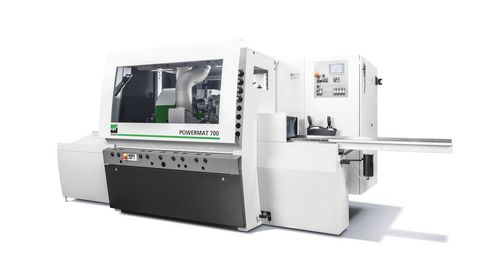
With the introduction of the SOLID PROFILE P series in the year 2004 WEINIG began a new era for planing and profiling. Now, with the SOLID PROFILE P 700 the next generation has arrived; offering undreamt-of possibilities.
The SOLID PROFILE P 700 is designed with a revolutionary new operating concept which no other moulder can offer. The result: improved ease of operation and very short setup times offer the highest degree of flexibility. With these outstanding qualities the new SOLID PROFILE P is the perfect response to the market demands of today and sets a new standard for four sided processing.
Different requirements - different prices
The price of a WEINIG machine is just as individual as your requirements are. Therefore, let us discuss briefly what is most important to you – you will then receive our preliminary, non-binding quote.
Personal advice – for higher productivity and greater efficiency
Together with your WEINIG expert you will find the ideal machine for your requirements. Simply submit the completed form, and your local WEINIG expert will be happy to discuss all further details with you.
The WEINIG SOLID PROFILE P series provides
- Innovative machine technology
- High production accuracy
- High level of work safety
- Modular design
- Made in Germany
Technical Details
Operating concept Comfort Set
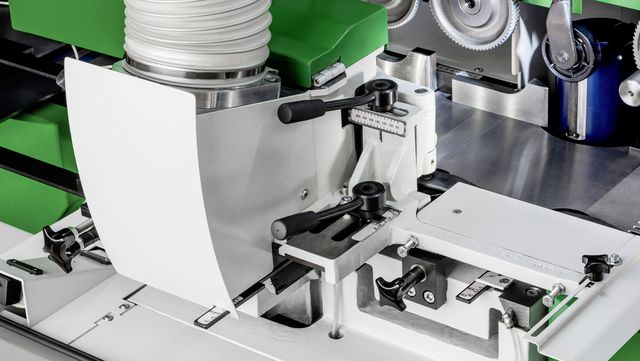
The new operating concept Comfort Set comprises a great number of wrench-free adjustments for pressure and guiding elements which can be performed quickly, accurately and without error. With features like this the machine operator will experience a new degree of comfort in performing the moulder setup like he never experienced before. The final proof of the new setup procedure can also be seen in the quality of the products you produce.
Performance
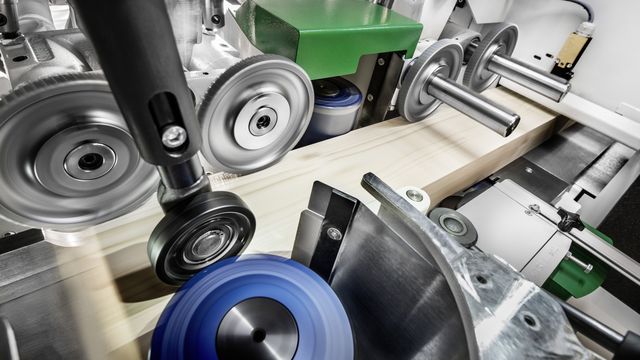
With 7,000 rpm spindle speed in standard the new SOLID PROFILE P 700 offers even more performance. This means more linear production every day without sacrificing high surface quality. Compared to conventional moulders, the production increase is up to 15%.
The option of 8,000 rpm spindle speed allows an even higher increase, which perfectly meets the current requirements in terms of productivity and cost effectiveness.
Options for extension
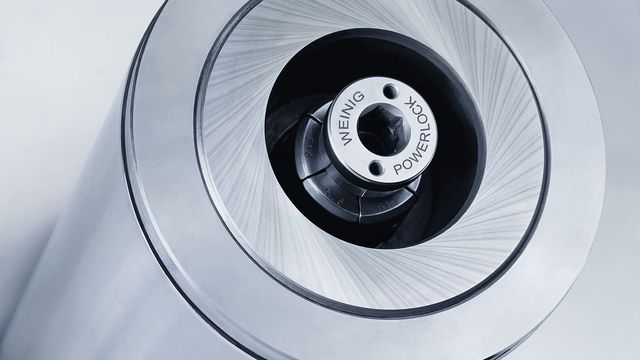
PowerLock
At the point where the cutting edge meets the work piece for cutting is where surface quality is determined. Precision tools are therefore essential. However, even the best tool needs spindles with perfectly true running accuracy.
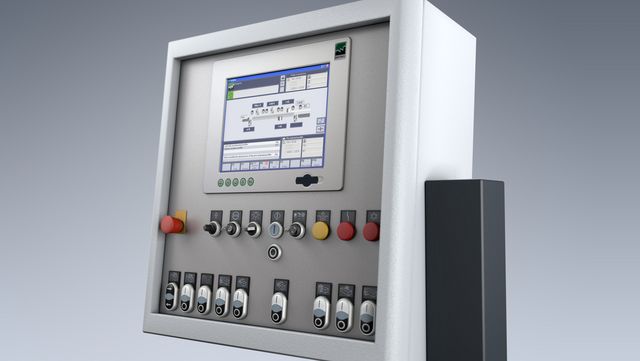
PowerCom Plus: Networked with your environment
Extremely high performance yet surprisingly simple - that is PowerCom Plus, the top solution for management and work organization of your SOLID PROFILE P 700.
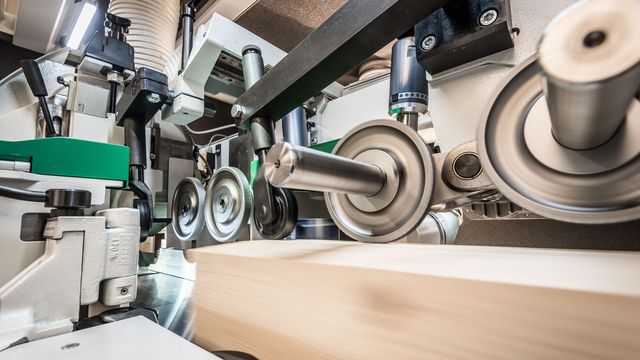
Pressure roller moving with the left spindle
Pressure elements and guides are responsible to guide the work piece smooth and safe through the machine. Therefore, they need to be setup properly. In this context, the pressure roller from above located opposite the left spindle and moving with the left spindle offers significant advantages.
References
Areas of application
Profiled mouldings
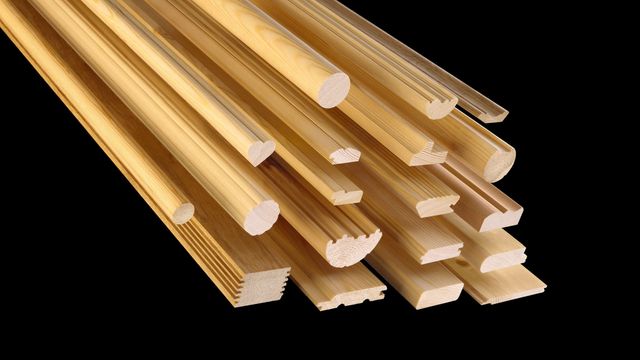
Our core competence
Profiling mouldings of all types has always been WEINIG’s core competence. Profiling includes a wide range of end products that nevertheless set the same challenges for machine technology: high levels of profile precision with excellent surface quality and regular cuttermarks.
WEINIG technology is always setting new standards in this area. The basis for this are the solid machine bases with precise machine tables and the fence at exactly the right angle to this. The superiority of the WEINIG machines is seen overall when dynamics are brought into the equation: spindles with high true running accuracy, a strong feed system and the corresponding pressure elements.
The perfect interaction of these components guarantees smooth transportation in a defined position through the machine. The result is the legendary WEINIG quality of your products: high profile precision, excellent surface quality and regular cuttermarks.
Window production
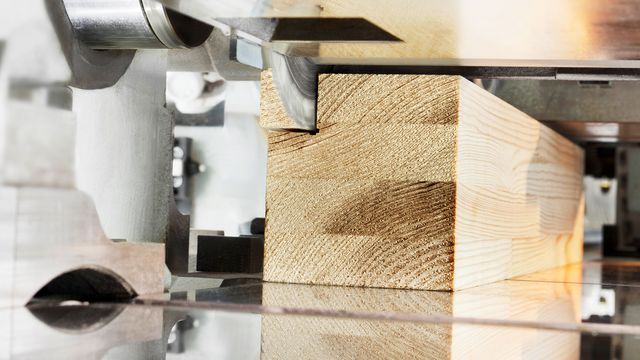
All stages of the processes on one machine
Profiling window scantlings on the long side and the cross side of the window scantling, and shaping and drilling are carried out on the processing center that outputs the fully processed scantling. However, the moulder still has an important role in window production as it is needed for 4-sided planing of the window scantling, to remove and to profile the blank glazing bead.
The WEINIG SOLID PROFILE P has a special window package that was precisely designed to complete these three process steps. Using the press of a button the user can select whether the four sides should only be planed or whether the blank glazing bead should be removed as well. Safety prompts ensure that an adjustment can only be carried out when there is no work piece in the machine and that there will be no collision between the saw blade and contact pressure elements. The PowerLock system means that the machine can be retooled in a very short time so that the glazing bead can be profiled.
The WEINIG system also enables the moulder to be connected to the cross-cut saw and the processing center. Thus, WEINIG offers the ideal solution for window production because it is the safest and most efficient.
Construction timber
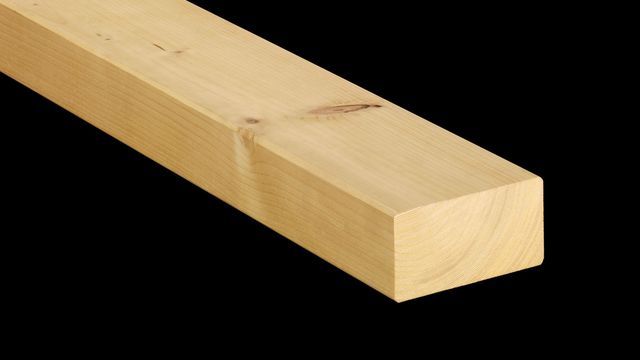
The importance of solid wood as a construction material has grown constantly over the last few years. This means that there are high demands on the surface quality, particularly for the visible areas. The largest area of application are beams, which are planed on 4 sides and chamfered.
Depending on your requirements, WEINIG offers the right solution, from a small machine to a large line; but they have one thing in common: a high level of flexibility because of the 90° chamfering unit.
The chamfering unit is used to produce the fourth chamfer on the beam after the other chamfers have been produced by the vertical spindles and the horizontal top spindle. The chamfering unit control means that dimensions can be changed quickly and a change in the strength of the chamfer can be made without changing the tool and simply by positioning the spindles.
With this technology WEINIG enables small companies to work with the same economy as a large organization.
Further information
Brochures
Simple, fast and sustainable: more details in a downloadable PDF document.
Download brochure